1. Process Digital Twin
Process twins, the superior digital twin types, combine system twins into a single entity to investigate system synchronization and cooperation. This system provides the most comprehensive picture of how things happen inside the factory or plant.
Therefore, it enables a far more in-depth and flexible output examination.
Process twins helps in:
Adjust inputs without disruption: Process twinning enables adjustments to factors like raw material feeding rate and manufacturing climate without impacting the manufacturing process or compromising quality.
Test predictions risk-free: Executives can simulate various business scenarios safely, avoiding reliance on intuition or theoretical assumptions.
Monitor KPIs efficiently: Provides real-time tracking of key performance indicators to ensure data-driven decision-making and improved operational effectiveness.
For instance, a process twin could simulate every aspect of the plant, even down to the workers running the machinery on the production line. In contrast, a system twin might simulate a manufacturing process.
Also read: How Digital Twin Platforms are Transforming Industries
2. System/Unit Digital Twin
System twins are copies of assets that show how multiple components come together to form functioning components at the system level.
System twins provide a:
Comprehensive view: System twins offer a detailed perspective of the entire plant or manufacturing facility.
Optimize systems: Enable testing of different system settings for maximum efficiency and uncover opportunities for new income streams.
Asset group focus: Cover a group of assets performing specific functions, such as primary product manufacturing or energy delivery.
Advanced capabilities: Go beyond detecting errors and breakdowns, providing continuous tracking and modeling for deeper insights.
Strategic decision-making: Facilitate tactical choices with complete process transparency and critical operational information.
At this level, continual tracking and digital twin modeling go beyond the primary digital twins' ability to detect errors and breakdowns. It is a route to obtaining information necessary for making tactical choices and achieving complete process transparency.
Meanwhile, to develop a successful outcome from this innovation, you must partner with the best digital twin companies.
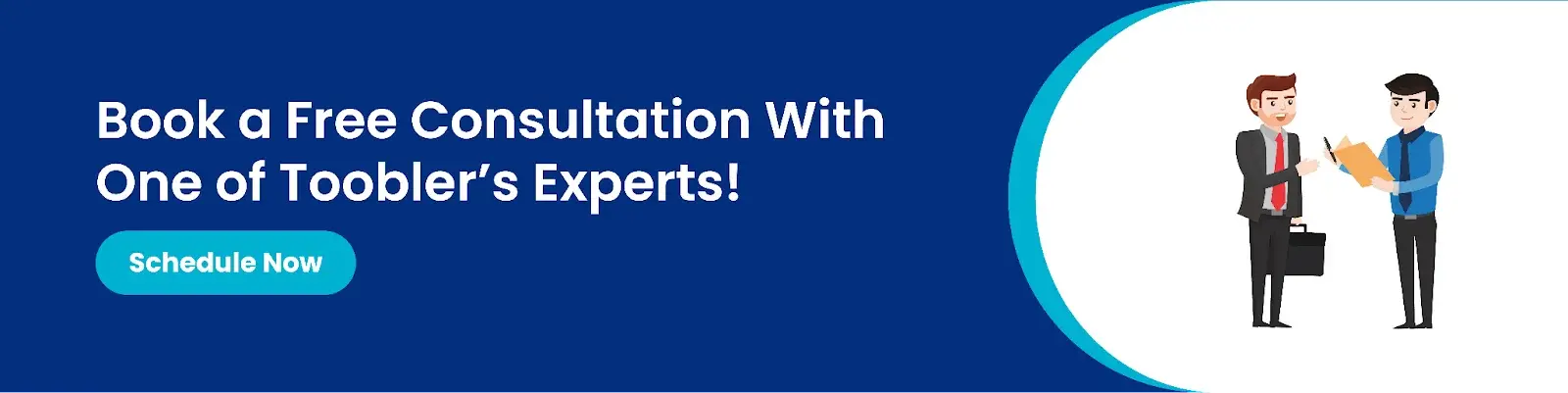
Big businesses mostly prefer process and system digital twins, with their increased complexity. This is because they are capable of financing long-term research and development initiatives.
Consequently, these businesses are able to achieve higher degrees of intelligent automation. They free up workers from overwork, reduce the number of defective batches, and optimize the use of water and electricity.
The system and process digital twins strengthen protection, or take complete control over their operations and production quality. These activities are primarily found in companies like Unilever.
Suggested read: Digital twin applications in various industries
3. Asset/Product Digital Twin
A product or asset digital twin is a digital replica of tangible assets such as machinery, buildings, and automobiles. It offers updated information on an asset's atmosphere, performance metrics, and functional health.
Product digital twin has the following characteristics:
Integration of component twins: Asset/Product digital twins combine multiple component twins or their data to model complex assets like engines, pumps, or buildings.
Performance analysis: Examine how components function as an integrated unit, identifying areas for optimization.
Enhanced efficiency: Help engineers identify improvement opportunities, reducing downtime and improving operational effectiveness.
Strategic insights: Provide valuable operational data, aiding in better equipment management and business innovation.
A good illustration of this situation is the compressed air solution maker Kaeser. This business tracked the amount of air that each of its items consumed using digital twin technology. Rather than offering their equipment for sale, they choose to bill clients based on the rate of air usage.
Please read: How much does it cost to develop a digital twin
4. Component/Part Digital Twin
The most basic type of digital twin technology is known as the component twin or parts twin. It is equivalent to the simplest components of the system, such as a particular piece of machinery or a product, like a sensor, switch, valve, etc.
Component digital twins has the following features:
Function monitoring: Sophisticated parts can have their functionality tracked and current conditions simulated using digital models.
Performance assessment: Evaluate reliability, durability, and effectiveness to ensure optimal operation.
Simplified factory representation: Part-level digital twins offer a basic resemblance to the factory architecture for focused monitoring.
Enhanced maintenance: Enable better equipment component monitoring, ensuring timely maintenance and reducing downtime.
Operational reliability: Guarantee consistent manufacturing operations and maintain the quality of the final product.
Further read: Why Digital Twins Are Key to Sustainability in Business
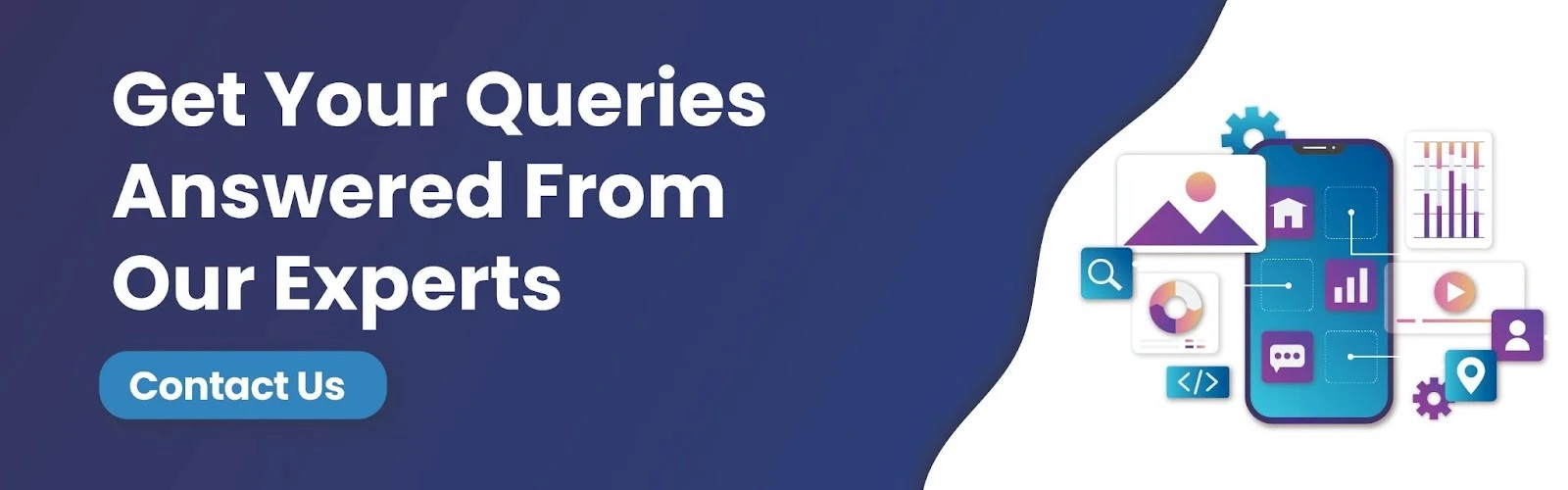